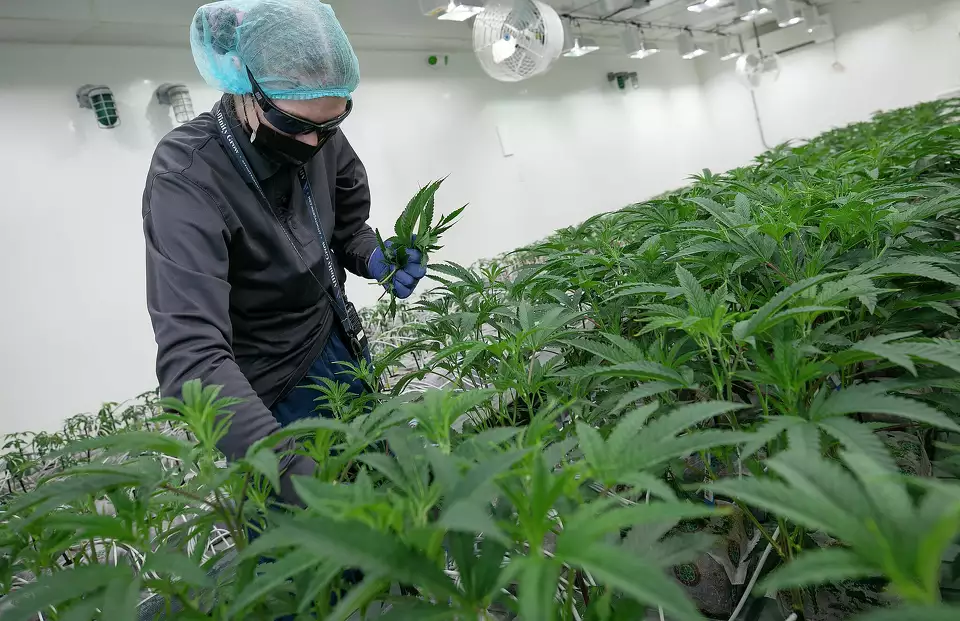
Once, when Rino Ferrarese was at UConn, the state police came into another dorm on campus, he recalled. He knew the friend of a roommate had some marijuana in his dorm room, but didn’t want to get involved.
He called his friend to warn him, he recalled, then said, “I’m going to the library.”
“I mean, we grew up in the ’80s with the War on Drugs,” Ferrarese said. “It was just a different way to look at the world. Different times. They were really bad times.”
Ferrarese began his career as a microbiologist, but he’s now managing partner at Affinity Grow in Portland, Connecticut’s first micro-cultivator of cannabis.
The facility has 10,000 square feet of grow space, the limit for a cannabis micro-cultivator in Connecticut. His last job was running the state’s largest cannabis cultivation facility, CT Pharma’s Rocky Hill site, which boasts 216,000 square feet of grow space, 26 times the size of his current venture.
Stephen Markle, who is working on developing various cannabis formulations, said “it’s like working for a craft brewery.” Markle also worked for larger cannabis facilities, including the largest in the country, in Las Vegas.
“It’s been enjoyable to not have to deal with what comes with being a publicly traded company,” he said. “To remain private, makes you more nimble.”
But it’s more meaningful than that for Ferrarese: “This is like one of my children,” he said.

Affinity Grow, the state’s fifth cultivation facility and first to open since Connecticut’s legal cannabis marketplace opened, began shipping products to Connecticut cannabis dispensaries and retail stores in October. The original four farms had been open since only medical cannabis was legal to sell.
They’re still getting started. Though Affinity, with which Ferrarese’s operation is partnered, has two retail operations, in New Haven and Bridgeport, the cultivation facility sells to any retail cannabis shop in the state, which puts them up against the largest “multi-state operators” growing cannabis in the country.
“It’s challenging because they have a lot more space,” he said. “An MSO like Curaleaf, they have a history.”
From seed to sale

At the moment, Affinity Grow is only producing flower, the actual plant matter which is then smoked or otherwise consumed. Eventually, the goal is to produce pre-rolled joints and gummies and baked cannabis goods and vape cartridges and more, but it’s a process that takes time.
“Eventually we’re going to get into formulating products, chocolates, tinctures, different types of oils, different textures and mouthfeels of oils,” Markle said.
The facility was purchased from CT Pharma — Ferrarese’s former employer — and licensed by the state last year. The first plants started growing in April 2023. The first plants were harvested five months later.
“We’re still identifying our great strains,” Ferrarese said. “Not all of these will be commercially viable and we won’t know until we go through the entire process.”
Cannabis strains are bought from breeders. Those plants are cloned, the seedlings are then grown, and then they take eight weeks to produce viable buds.
“Then we have to dry the flower out and we have to test it,” Ferrarese said. “Results come back, it might be almost three and a half months before we know how potent or how viable ‘Hippie Crasher’ is as an industrial strain.”

Plants are moved from room to room as they mature; each step of the process designed to trick the plant into believing it’s a specific season or time of day. The humidity levels are controlled precisely, as is the spectrum of light shining down. A blueish hue helps the plants think it’s fall or winter. An orange hue convinces them that it’s summer, and time to produce buds, heavy with THC.
Even though every plant began as a cutting from a “mother” plant, there’s no guarantee that they will be identical in look, taste or chemical makeup. Ferrarese said the DNA is just a “genetic road map.
“So, These all came from the same plant,” he said, gesturing to a tray of 5-inch-high seedlings. “They might have come from two different ‘Hippie Crashers,’ but both came from the same plant. But there is some variation, different expression where you’re taking the cutting of the plant, either the top, the middle of the bottom.”
“Variation is the spice of life. Evolution is driven from that variation,” he explained. “The top of a plant is where it produces the flowers. The bottom of plants where you produce fruits. So if you take cuttings closer to the bottom, you might have more DNA in that segment that drives that process versus the other process.”
As a micro-cultivator, Affinity Grow is currently the only licensed business in Connecticut legally allowed to sell seedlings, but they’re not at that point just yet. Connecticut residents are legally allowed to grow six plants — three mature and three immature — but Ferrarese doesn’t want to sell any duds.
“We’ve been sort of working toward making cuttings available. We’re going to offer them to the market. We want them to be reliable. We want the customers to be successful,” he said. “When you buy plants at Home Depot or even a garden shop, you have certain expectations when you bring the plant home that it’ll be alive after six months or a year or so. We just want to make sure that we set up any customer who buys our cuttings or seedlings with the highest likelihood of success.”
A ‘family’

Caitlyn Rutherford has been in Connecticut for a year now. She came to the state from Kentucky specifically to learn about the cannabis business. On a recent afternoon she was found trimming leaves off plants just about ready to be harvested.
“I came here specifically for marijuana because it’s not legal in Kentucky,” she said. “I came here because this is the career I was most interested in, and my aunt and uncle live here so it gives me way more opportunity.”
She said she’s happy working in a smaller operation because it’s “a nice community.”
“People that I work with are like a team, or a family,” she said.
Rutherford does not spend all her time trimming plants but works where she is needed. There are only 29 employees in the whole operation, so everyone wears several hats.
Ferrarese, for example, is the managing partner and a part owner. He personally hired every employee and is often on the floor, overseeing every part of the cultivation process, in part because there’s a lot at stake.
“Rarely are things as simple as they may appear at first blush,” he said. “It’s perishable. So, if something bad happens at the clone stage, we’ll just get more clones. Well, are the moms big enough to donate them?”
“If the lights stay on in a room when they’re supposed to be off, it could potentially stress the plant — female plants that are producing flower, to create colonies, self pollinate, and then that drives seed production,” he said. “Nobody wants flower with seeds now. That could be devastating.”
A growing cannabis business

Affinity is still figuring out what works and what doesn’t. On a recent visit, one room contained 140 “Hippie Crasher” plants, 34 of the “Apples and Bananas” strain, 26 “Bachelor Party” plants and 120 plants producing the cannabis strain known as “Italian Ice.”
“Before we dive into the deep end with them, we’re doing smaller counts,” Ferrarese said. “If these end up being really good strains, then we’ll say, ‘Okay, maybe we’ll do 140 of these next time.’”
Affinity Grow, though, is not yet a profitable business. They paid $4 million for the building, spent $2.5 million on renovations and then had to wait until final approval from the state, from the Department of Consumer Protection and the Social Equity Council.
“In the meantime, we have employees coming to work,” Ferrarese said. “They’re not growing cannabis, they’re setting up the facility.”
That means every decision is important.
“How many plants should I put in a cloning tray? How many trays do you have in a room? How big does my room need to be?” Ferrarese said. “You definitely have all these factors and, probably, it takes about two or three years before you really start understanding the potential for your business.”
And any cannabis business in Connecticut is, of course, interconnected with every other cannabis business in Connecticut, and they are all impacted by the national and global economy. That, Ferrarese said, is why cannabis cultivation facilities have been slow to open in the state.
“Financially speaking, investors are cautious,” he said. “It’s a tough time right now to try to raise and raise capital, especially for projects like this … it is an 18-month build out, and … now that we’re built out, now we have to plant crops. (It takes) six, eight months until you have a product that’s viable that you can sell. And how long until you’re cashflow positive? Now you’re two and a half, three years into the venture.”
H/T: www.registercitizen.com
Read The Whole Thing By Clicking Here